There’s a reason we talk about safety so much at B&W Energy Services. Our team is committed to providing the products and services that meet the needs and expectations of our customers while simultaneously achieving the objective of Zero Safety Incidents. There’s a lot that our team manages behind the scenes to secure this goal, keeping your team and ours safe while providing your facility with unmatched pre-commissioning and commissioning services. Here’s how we do it.
At B&W, we hire and train responsible professionals who know how to lead a team in safety. As leaders in the industry, our team accepts the direct responsibility for health and safety matters in our control, overseeing the implementation of safety and quality standards amongst contractors we supervise both directly and indirectly. Plus, we deal promptly with employees’ health and safety concerns and make sure they’re fully aware of any known hazards on-site. Before they arrive, we evaluate each project and work to mitigate all hazards in advance.
In conjunction with monitoring the standards themselves, our managers ensure that their team is also equipped to look out for policy execution. We transfer knowledge of all duties and obligations under relevant legislation and client requirements, so we know our team knows what’s ok on site and what’s not.

It’s vital to us that we enforce our policies beyond just our team—any contractors, suppliers, vendors or other visitors to a work site must adhere to B&W’s guidelines at all times. We perform workplace inspections and investigate accidents or incidents promptly and often, and if any incidents occur, we immediately create corrective plans to ensure similar situations aren’t repeated. Our Health, Safety and Environmental (HSE) communications procedure is designed to eliminate miscommunication across our organization, from the bottom-up and top-down, so B&W can attain our goal of zero safety incidents.
One of the ways we keep up with safety standards is through our Quality Management System (QMS), which not only provides a framework for establishing and reviewing quality objectives but also serves to continually improve the B&W overall management system. We’re committed to ISO 9001:2015 quality standards, and the QMS is a never-ending cycle of continual improvement, preventive actions, corrective actions and suggestions to achieve our objectives.
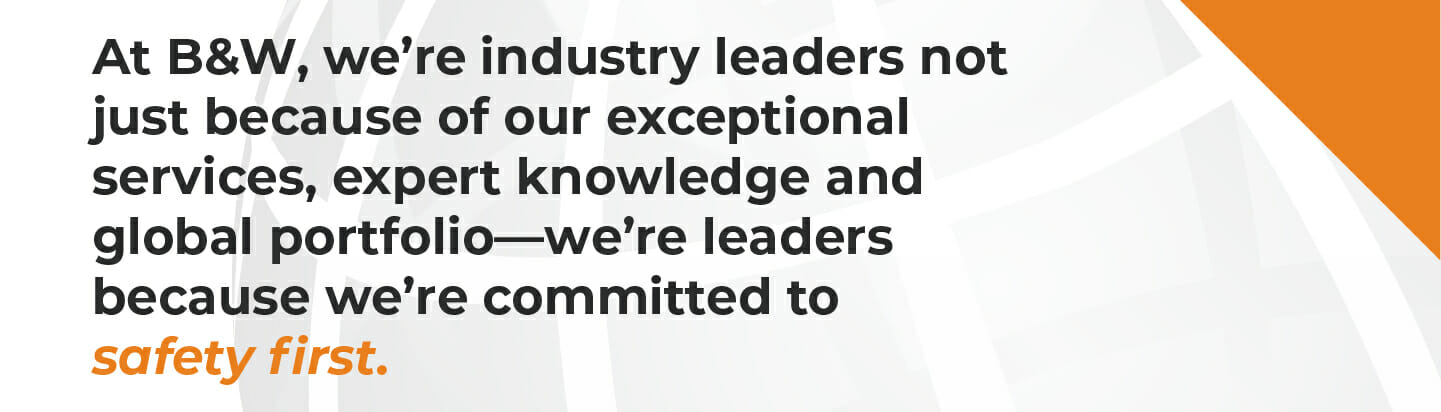
B&W has a dedicated HSE manager, Edward Dill, who’s responsible for ensuring corporate HSE policy is effectively communicated and enforced throughout the company, and we assign a field project manager onsite to facilities to assist with these responsibilities. We have several systems and actions in place to make sure things are getting done safely at our project sites—we use project kick-off meetings, service procedures, job hazard analyses, toolbox safety meetings before each shift, weekly safety meetings, job site hazard assessments, health and safety inspections, health and safety audits and suggestion boxes to make sure no stone is left unturned. If there’s something happening at a site that’s even just slightly deviated from our safety system, we correct it as soon as possible.
At B&W, we’re industry leaders not just because of our exceptional services, expert knowledge and global portfolio—we’re leaders because we’re committed to safety first. Whether you’re partnering with B&W for AquaLazing, chemical cleaning, air blows or a mix of all of our pre-commissioning services, you can be sure that we’re delivering what you need while keeping your team, and ours, as safe as possible.
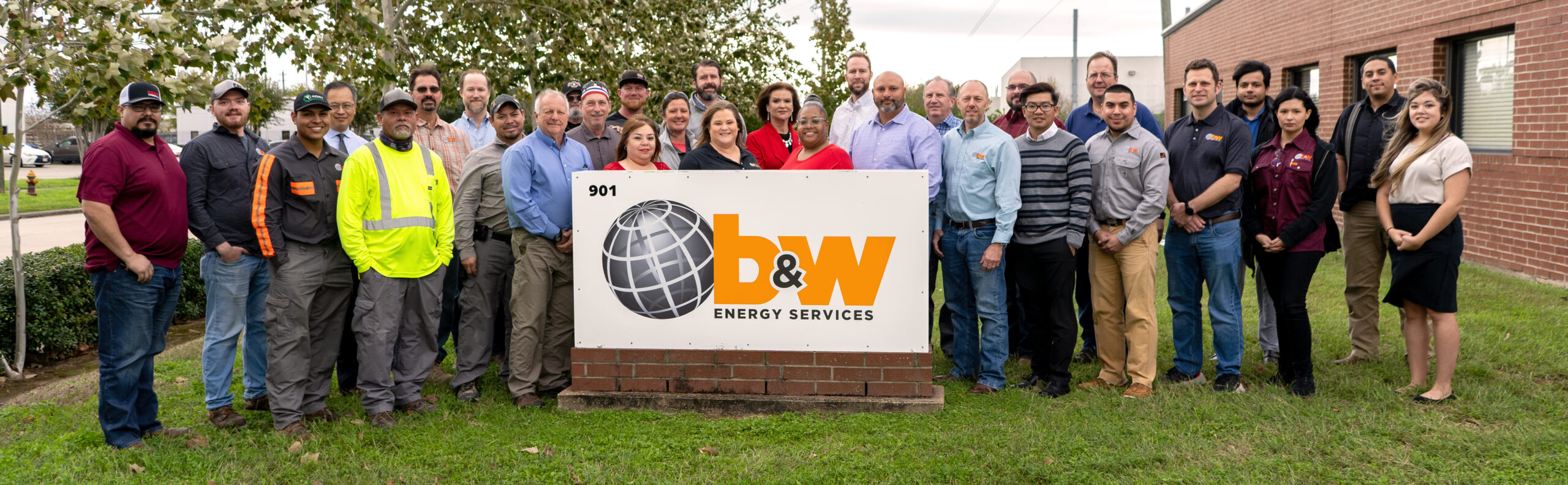