What is Chemical Cleaning?
Chemical cleaning uses chemical solutions to remove organic material, oils, grease, mineral deposits, iron and other matter from the interior of systems. Depending on the specific needs of the project, chemical cleaning of pipes or chemical cleaning of a boiler can look a few different ways. It may involve the injection of chemicals into boiler water during firing, use of external flushing equipment and a heat source, or a combination of chemicals with a flow of steam. The chemicals used in the chemical cleaning process vary depending on the type of buildup and the material of the piping system. Acid-based cleaners are commonly used to remove rust and scale buildup, while alkaline cleaners are used for removing grease and oils.
Why is Chemical Cleaning Important?
The chemical cleaning process plays a vital role in maintaining the safety, efficiency and durability of large-scale industrial projects. As time progresses, corrosion, scale and other impurities build up within systems, resulting in reduced performance and costly shutdowns. Chemical cleaning methods help ensure that piping systems stay structurally intact and unobstructed.
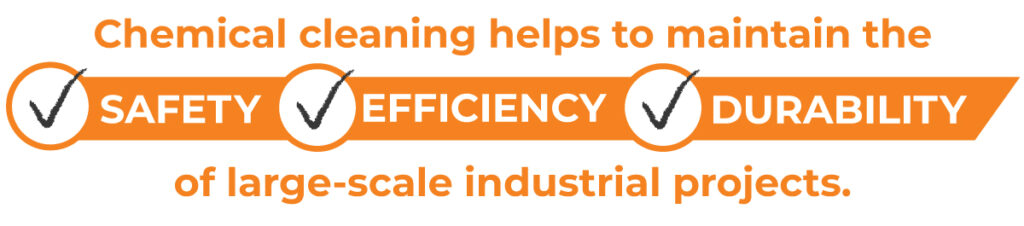
Pre-Operational Cleaning vs. Post-Operational Cleaning
Most forms of chemical cleaning fall into one of two categories: pre-operational cleaning and post-operational cleaning. Pre-operational cleaning is performed following construction activities to prepare equipment and facilities for operation by removing any materials that could interfere with performance. Post-operational cleaning may be performed for a variety of reasons, including an observable reduced heat transfer or flow rate following production, increased access for more thorough inspection or to address safety concerns. Some of the most commonly performed chemical cleaning procedures include degreasing only, boiler boil-outs and acid-based chemical cleaning.
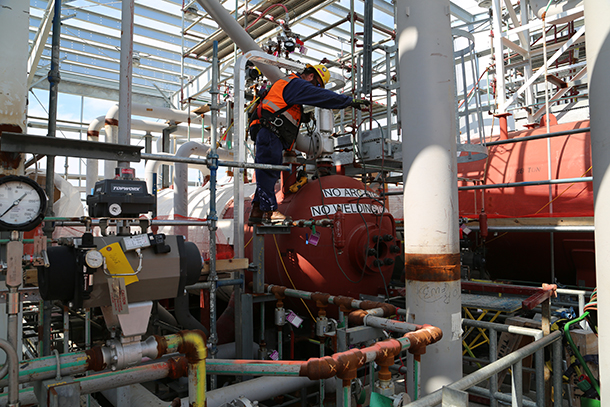
What Is Degreasing?
Degreasing removes excess oil, grease, lubricants and other foreign matter from piping, process equipment and steam-generating equipment. Although there are various degreasing methods, the process typically involves an external heat source and temporary circulation pumps.
Which Degreasing Method Should You Use?
The appropriate degreasing method for your project depends on the kind of equipment you’re cleaning and the material it’s made of. Several degreasing techniques include forced circulation and natural circulation like in a boiler boil-out. Degreasing is commonly applied to amine systems, critical oxygen gas systems and some steam-generating equipment.
What Is A Boiler Boil-Out?
Following the manufacturing process, newly installed boilers are often slick with oil, grease and organic material from the boiler’s internal components. If these coatings aren’t removed, they may reduce the boiler’s heat transfer rate and cause tubes to overheat and burst. Due to the risks that contaminants pose to equipment, conducting a boil-out is essential to thoroughly cleanse a boiler.
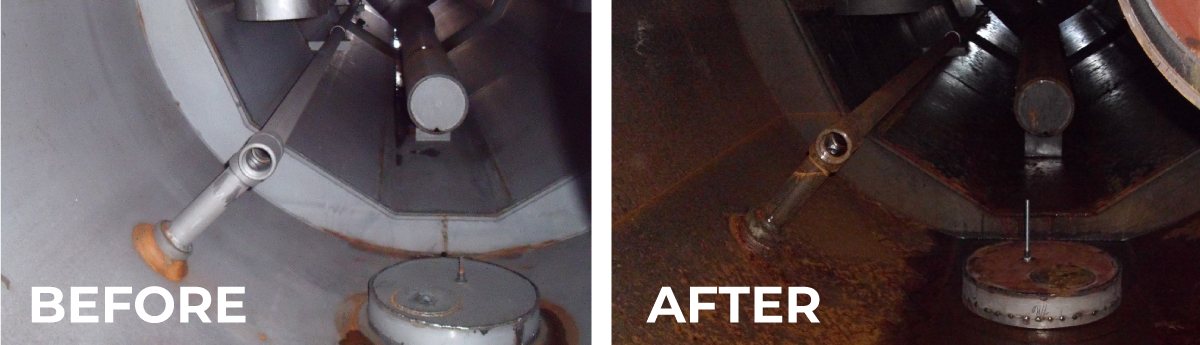
To decontaminate a boiler, B&W injects a chemical cleaner with a high pH directly into the boiler water to thoroughly degrease and passivate internal surfaces. The heat accelerates the boiler chemical cleaning process as the solution recirculates and dissolves any grease or oil within the boiler’s internal systems. While a boiler boil-out can technically be classified as a degreasing process, degreasing is typically a standalone process using external pumps and equipment. Boiler boil-outs commonly apply to smaller package boilers, HRSG cleaning or other lower-pressure steam-generating equipment. B&W typically performs this on college campuses or other CHP-type projects.
What is Acid-Based Chemical Cleaning?
Acid-based chemical cleaning is commonly applied to high-pressure steam-generating equipment and critical piping systems to remove corrosion, scale and other materials from the interior of systems. It is commonly combined with a degreasing process in a single volume fill to reduce the amount of waste effluent generated during cleaning.
The most common pre-operational chemical cleaning method uses a citric acid-based chemical blend for new equipment to remove mill scale, rust, preservatives and other materials from its surfaces. Once cleaning is complete, an oxidizing agent is used to passivate the metal surfaces to provide protection against further corrosion until the system is put into service. Additional preservation methods, such as introducing nitrogen to the system, may be used if equipment startup is delayed.